Introduction to PET Bottles:-
Plastic Bottles nowadays is something that is in high demand, is it mainly because of its durability. Majority of people around the world use it in a daily basis. Containing innumerous uses, plastic bottles or plastic to be specific, must be one of the greatest discoveries in the recent centuries.
About Polyethylene terephthalate used for Bottling:-
Polyethylene terephthalate is not made is not made in a single process. It is made by the reaction of two chemicals known as Purified terephthalic acid (PAT) and ethylene glycol (EG).
These two chemicals form Polyethylene terephthalate along with other types of plastic, used in variety of applications such as engineering, nylon production, etc.
Below are some Properties of Polyethylene terephthalate:
- Density: 1.38~1.40g/mm3
- Melting Temperature: 254-256°C
- Crystallinity: >=45%
- Glass Tempurature: 82°C
PET is a long chained molecule with the repeating unit displayed above, resin, a bluish white substance, is made from poly condensation of terephthalic acid and ethylene glycol. Resin manufacturers supply PET in the form of small pellets, each weigh about 0.05 grams.Being transparent, PET can reach a tensile strength of about 1/3~1/2 of steel's.
The number of PET repeating units per chain, used in the bottle industry to make plastic bottles is about 100 to 155, usually labeled in terms of resin IV.
Main Advantages of PET:-
- Pure – PET does not involve, by reacting with the food or beverage which is kept within the container. Therefore, PET complies with international food contact regulations.
- Lightweight – 10 times, lighter than a glass pack, PET bottles, hence, reduces shipping costs by 30%. If a glass and PET bottle having the same size is compared in volume it can store, PET will come in first, as its wall is thinner.
- Crystal Clear – The product looks clean and healthy and in physical good shape. These attract attention and increases the sales of the products contained within it.
- No Leakage – Due to the absence of a weld line in the bottom the Mineral Water bottle preform leakage does not occur.
- Design Flexibility – Can be designed in all shapes and sizes, designs and colors.
- Recyclable – As it is one single material, PET bottles can be washed and crushed into flakes and remolded into shape. It has other uses after it is recycled such as for strapping, making carpets, etc.
Production of PET bottles
Usually PET bottles are manufactured using 2 different methods.
These are :-
- One-Step "hot perform" method.
- Two-Step "cold perform" method.
Step-one "hot perform" method
This method is just one step, from PET granule to finished bottles, all the processors are done in one integrated machine. That is from the injection mold of the preform to the removal of the preform from the injection cavity, and to stretch blow the preform to a bottle all in one machine, while the temperature remain constantly high for the whole process as injection molding and blow molding, the material should in an elastic form. This method saves a lot of energy as the material only has to be heated only once, that is when it is injected to the cavity to produce the preform. The One-Step method is commonly used in small or medium PET production companies.
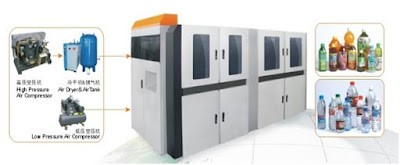
Step-one "hot perform" method:-
This method is just one step, from PET granule to finished bottles, all the processors are done in one integrated machine. That is from the injection mold of the preform to the removal of the preform from the injection cavity, and to stretch blow the preform to a bottle all in one machine, while the temperature remain constantly high for the whole process as injection molding and blow molding, the material should in an elastic form. This method saves a lot of energy as the material only has to be heated only once, that is when it is injected to the cavity to produce the preform. The One-Step method is commonly used in small or medium PET production companies.
Step-two"cold perform" method:-
This method has 2 distinct machines to perform the injecting and blow moldings. The preform is injected into shape on the first machine, and then the preform is reheated as the it isn't brought directly to the blow molding machine and blown on the second machine.

This method is not very efficient as the heat lost is considered as a loss of energy. But this machines are fully automated.This method is used in most medium to large scale PET production companies.This machine is 200% more efficient than the one-step machine.
Possible Defects while production of PET Bottles:-
One of the Major defects in the production of PET Bottles is the production of Acetaldehyde.
This compound also called as AA, is the taste of an acidic taste in most citrus fruits. This taste in the bottle can ruin the taste of the drinks, especially if its water as the taste of pure water isn't strong enough to disguise the taste of AA, unlike the sweet flavors. If the presence of the AA is noticed the quality of the product literally, goes down the drain.
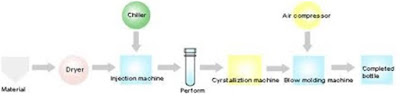
AA is produced along with the PET when the temperature of the material is higher than 260°C, this temperature is reached inside the injection molding of the preforms, therefore is the process is not maintained correctly, AA is produced along with the
PET preform.
Decreasing the melt temperature and the residence time and help reduce the production of AA.
Other forms of defects are briefly mentioned below.
- OH- or COOH- end groups doesn't becomes non-reactive.
- Amount of poly-functional macromolecules increases.
- Hydroxide and peroxide groups build up at the surface of the PET and etc.